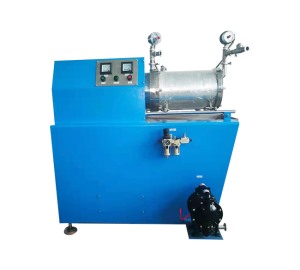
20LOrdinary Sander
Product Introduction
The ordinary Sander is a grinding machine with wide adaptability to raw materials and high efficiency at the present stage. The grinding chamber is narrow, the rod gap is small, and the grinding kinetic energy is concentrated. Integrating the cooling system and the full-automatic control system, it can complete the continuous production and processing of raw materials and improve productivity.
Sander, also known as ball mill, is mainly used for wet grinding of chemical liquid products. According to performance indicators, it can be roughly divided into horizontal Sander, basket Sander, vertical Sander, etc. The key is composed of the human body, grinding cylinder, sand and stone roller (lever), grinding medium, motor, and supply pump, and the supply rate is controlled by the supply pump. The grinding medium of this machine and equipment is generally divided into zirconia beads, glass beads, Zirconium(IV) silicate beads, etc. Compared with cement ball mill, roller ball mill, micro powder machine and other grinding machines and equipment, the Sander has the advantages of high production efficiency, low cost, and high product fineness. There are significant differences in processing technology standards, which can adjust and classify the fineness regulations of grinding media.
Vertical Sander, lithium battery Sander, horizontal Sander, basket Sander, double cone rod Sander and horizontal Sander are common. Except for ordinary 2-3/3-4mm glass beads, other machinery and equipment use 0.8-2.4mm zirconia beads. The Sander adopts axial force disc grinding structure and is arranged in order. This system overcomes the disadvantage of traditional grinding machines with uneven distribution of grinding media, allowing for significant kinetic energy transfer and high grinding efficiency. Adopting a two end forced refrigeration machine seal, with excellent sealing performance and excellent operation. The separation system adopts a high flow rate LDC dynamic gate gap separation equipment, and the feed inlet is not easily blocked under high flow rate standards. The total area of overcurrent is 0.05-2.0mm, which can be used as a grinding medium above 0.1mm.
The grinding machine adopts a disc type or rod pin type, with a closed inner wall design scheme. The mill is installed on the mixing shaft in sequence, which overcomes the shortcomings of traditional vertical grinder, such as uneven grinding media and poor Particle size analysis behind the grinder. Under the function of the feed pump, raw materials are fed into the grinding machine. The design scheme of the inlet is to push one end of the connecting flange plate and reverse it with the reverse bottom of the rolling bearing of the mechanical equipment. The mechanical seal of silicon sand mill has a bearing capacity and a long service life. In the high-speed operation of the mixing shaft and force plate, the relative velocity of the compound between the raw material and the grinding medium. Therefore, the solid particles of the raw materials are dispersed, cut, and ground, and the product is obtained through a filtering device that separates the rotor gaps of the dynamic large flow motor. According to the product grinding technology, mass grinding and serial grinding technology can be used.