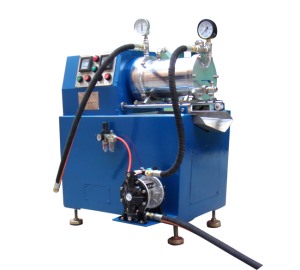
Ordinary Blade Sander
Product Introduction
Characteristics of ordinary blade sanding machine:
1. The design is simple and easy to operate, with low maintenance costs and wide application industries.
2. Adapt to continuous or mass production, with a fully enclosed structure.
3. Temperature, pressure, automatic protection device, automatic shutdown in case of malfunction.
4. Separate dynamic separation and intermittent screen dynamic separation, capable of high flow discharge without blockage.
5. Mechanical seals and perfluorinated rubber seals are used to stabilize the equipment.
6. The inner tube set structure is convenient for replacement, and different materials can be selected.
At present, the Sander is a grinding equipment with wide material adaptability and high efficiency. The grinding chamber is narrow, the clearance between the paddles is small, and the grinding energy is intensive. With the cooling system and automatic control system of the performance, it can realize the continuous processing of materials and continuous discharging, increasing the production efficiency.
Ordinary vane Sander adopts eccentric disc grinding structure and is arranged in sequence. This system overcomes the disadvantage of uneven distribution of grinding media in traditional grinding machines. Automotive paint Sander enables the energy transmission of grinding media, with high grinding efficiency. It adopts double end surfaces with forced cooling mechanical seal, which is well sealed. The separation system adopts large flow LDC dynamic grid slot separator, which will not block the outlet under large flow conditions, The overflow area reaches, with a gap range of 0.05-2.0mm, and grinding media above 0.1mm can be used.
The ordinary vane Sander adopts the closed design of eccentric disc grinding chamber. The grinding disc is installed on the mixing shaft in sequence, which overcomes the shortcomings of the traditional horizontal Sander, such as uneven distribution of grinding media and poor particle size distribution after grinding. Materials enter the grinding chamber under the action of the feed pump. The inlet is designed to drive the end of the connecting flange. The flow direction of materials and the mechanical bearing are opposite to the bottom end, which greatly reduces the bearing pressure of the mechanical seal, In the high-speed operation of the eccentric disc of the mixing shaft, the mixture of materials and grinding media moves relatively. As a result, the solid particles of the materials of the silicon carbide Sander are dispersed, sheared and ground, and the products are obtained after passing through the dynamic large flow rotor gap separation filter. Depending on the grinding process of the product, separate batch grinding or series grinding processes can be used.