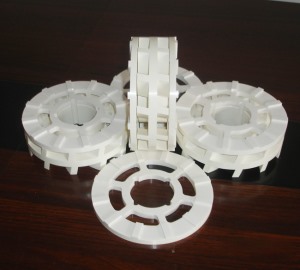
Nano Sanding Machine Structural Components
Product Introduction
(1) The development of ceramic Sander grinding medium separation system is accompanied by the continuous improvement of commodity fineness regulations, and the specification of applied grinding medium is becoming smaller and smaller. The separation of small size grinding media is one of the difficult problems in the research and development of Sander products.
The clearance ring (small total overcurrent area) and static data screen used in traditional Sander are difficult to separate small size media! Therefore, more and more dynamic centrifugal separation systems are being applied. The Centripetal force caused by the separation rotor pushing the medium to rotate causes the medium to be thrown to the outer periphery of the rotor, while the rotor is mainly slurry. When the separation screen is arranged on the rotor, the material can be discharged smoothly according to the screen clearance, which is not easy to cause blockage and damage. Therefore, applying the basic principle of dry cyclonic separation to the medium separation of Sander is the leap of the development trend of Sander!
(2) Relative density pin bar Sander
In the past, many key Sander manufacturers felt one-sided; For commodity fineness (reduce particle size), ceramic Sander can increase specific energy! As a result, many pin bar Sander with complex structure have occurred.
The Sander structure-1 is densely arranged with many carbide pins on the rotor and stator. The raw materials enter from the top and are then discharged from the bottom through a "N" shaped line that undergoes twists and turns/collisions. The damage to the pins, rotors, and stators caused by the medium is quite severe, and raw materials are usually contaminated by metal materials. And only zirconia grinding medium should be used.
The Sander structure-2 is basically the same as structure-1, but in order to better handle the heat dissipation problem, a refrigeration jacket is set on the rotor.
The Sander is equipped with pin bars on the rotor and refrigeration jackets on the stator and most of the rotor. The pin rod has severe damage to the inner surface of the stator directly opposite it, and metal material contamination is inevitable!
(3) Vertical centrifugal Sander relative density outer ring grinding area
After many years of misguided and complicated design scheme of Sander due to human factors, we finally returned to our roots! Discovering that the grinding of raw materials occurs in grinding areas with specific energy (just bustling). The relative density zone only occurs in the outer ring area with high online rates.
The Sander is fed axially from the outer stator, and the raw materials passing through the outer ring grinding area are discharged axially and laterally according to the dynamic medium separation screen.
The raw materials of the Sander go through the side of the hollow shaft to the rotor and arrive at the outer ring grinding area. The drum (stator) of the machine equipment rotates at a different speed from the inner rotor. The medium separation screen (fixed on the drum) becomes a rotating dynamic separator, and the complex dual rotor structure has high requirements for the parallelism deviation of each rotating body.
The raw materials of the laboratory Sander are added radially to the outer ring grinding area, and the raw materials after grinding are discharged according to the outer ring screen ring. Grinding the track, also known as the ceramic separation ring. Although the total filtration area has increased, the separation ring is severely damaged and easily blocked.