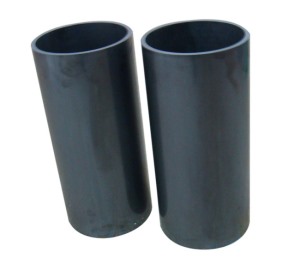
Silicon Carbide Inner Cylinder
Product Introduction
Ordinary sand mill silicon carbide wear-resistant materials generally use quartz and crude oil coke as key raw materials. They go through mechanical processing and manufacturing in the material preparation process, becoming the particle size distribution, and then according to chemical calculation, they are mixed into furnace charge. Wear resistant materials should be used to adjust the exhaust level of the furnace material, and appropriate wood chips should be added when mixing the furnace material. When refining green silicon carbide, appropriate salt needs to be added to the furnace charge.
The furnace material is installed in an intermittent electric heating furnace. The electric heating furnace has end walls on both sides and graphite electrodes near it. The furnace activated carbon fiber is connected between the two electrodes. The furnace core is surrounded by furnace materials that participate in the reflection, while the outside is insulated and insulated. During smelting, the electric furnace is powered and the temperature of the furnace core increases to 2600-2700C. Electric heating is sent to the furnace material based on the surface of the furnace core, causing it to slowly heat up. When it reaches above 1450C, chemical changes occur, converting it into silicon carbide and escaping carbon monoxide. With the change of time, the high-temperature range of furnace materials continues to develop, and more and more silicon carbide is produced. The rod nail Sander is continuously generated in the furnace, volatilizing and moving, and the crystal grows into a cylindrical crystal cylinder. The inner wall of the crystal cylinder gradually dissolves after reaching 2600C due to high temperature. The dissolved silicon is then fused with the carbon in the furnace charge to form new silicon carbide. In the early stage of furnace self power transmission, a key part of electric heating is used to heat the furnace material, while the heat generated for producing silicon carbide is only a small part. In the middle and later stages of power transmission, a large proportion of the commonly used heat generated by silicon carbide is generated. In the middle and later stages of power transmission, heat loss accounts for a crucial part. Adjust the correlation between power output and time, select the power outage time, in order to achieve good electrical heating utilization rate. High power resistance furnaces generally choose a power transmission time of around 24 hours for easy work distribution. On this basis, adjust the correlation between the output power of the electric furnace and the furnace specifications and models.
During the entire process of electric heating furnace power transmission, in addition to the basic reflection of producing silicon carbide, various impurities in the furnace material also undergo a series of organic chemical and physical transformations, resulting in deviations. The same goes for table salt. The furnace material continues to decrease throughout the entire smelting process, and the surface deformation of the furnace material moves downward. The carbon monoxide generated by the reaction is diffuse in the air, becoming a hazardous component of the surrounding air that pollutes the environment.
After the power outage, the entire process was basically completed. But because the furnace is very large, the stored heat is very large, and it cannot be cooled temporarily. The temperature inside the furnace may cause chemical changes, so there is still a small amount of carbon oxide escaping from the furnace surface again. For high-power electric furnaces, continuous residual reactions can reach 3-4 hours. The response at this time is insignificant compared to the response during power transmission. But due to the fact that the surface temperature of the furnace had already decreased at that time, the combustion of carbon monoxide was insufficient. From the perspective of labor protection, ink Sander should still be highly valued. After a period of cooling after a power outage, the furnace wall can be dismantled, and then the raw materials inside the furnace can be gradually removed.